With over 100 years of experience and expertise in the industry, Berco manufactures and supplies undercarriage components to the world’s leading heavy machinery OEMs and to the Aftermarket. Renowned for the quality of its products, Berco’s reputation is further bolstered by its dedication to providing tailor-made and innovative solutions for applications that operate in both unique and extreme conditions. Francesco Grenzi, Executive Director of R&D reveals some of the company’s most recent innovations that operate in particularly demanding surroundings.
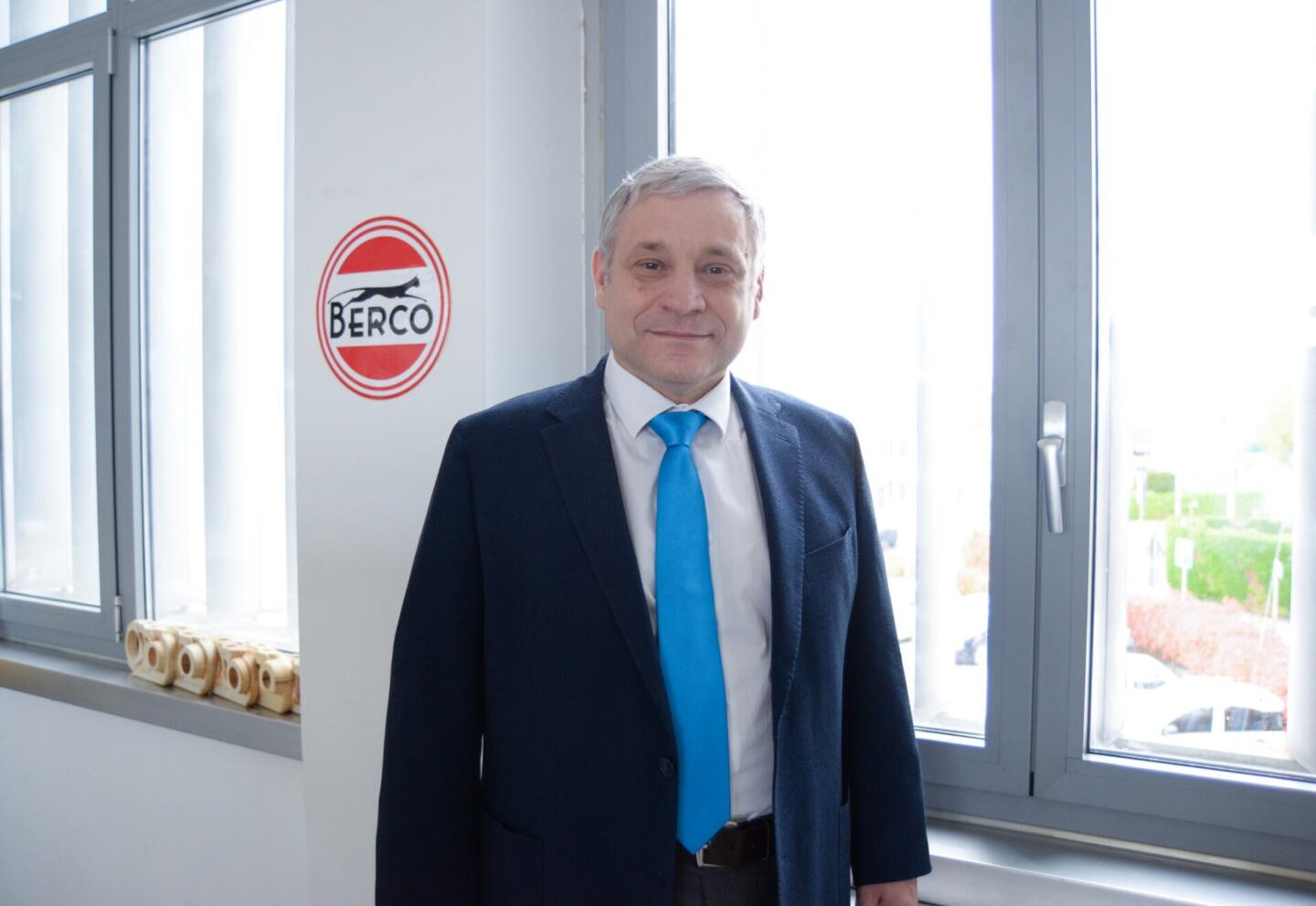
Robustus featuring BPR2
Robustus (ROtating BUShing Undercarriage System) and BPR2 (Berco Positive Pin Retention2 System) are two recent innovations from Berco that symbiotically deliver even more benefits to the customer. Robustus is a specially engineered system that is used D5 and D6 class dozers. The ‘Rotating Bushing’ system, in conjunction with BPR2, increases the life of the lubricated track group assemblies in applications operating in highly abrasive terrain; thus, reducing ownership and undercarriage costs. This is of particular pertinence for owners of heavy machinery, given the fact that the undercarriage accounts for 50 percent or more of the total lifetime cost of a machine (maintenance and downtimes).
The advantages of this connected system have even convinced one of the leading manufacturers in Europe and the US to have it fitted as original equipment (OE) on some of their 150 to 250 HP range dozers, as of January 2021 (for both standard and rotating bushing versions designed for especially demanding work).
Now in its third generation, Robustus is fully compatible with existing frames and standard components of D6 and D5 classes; the conversion, moreover, can be performed easily.
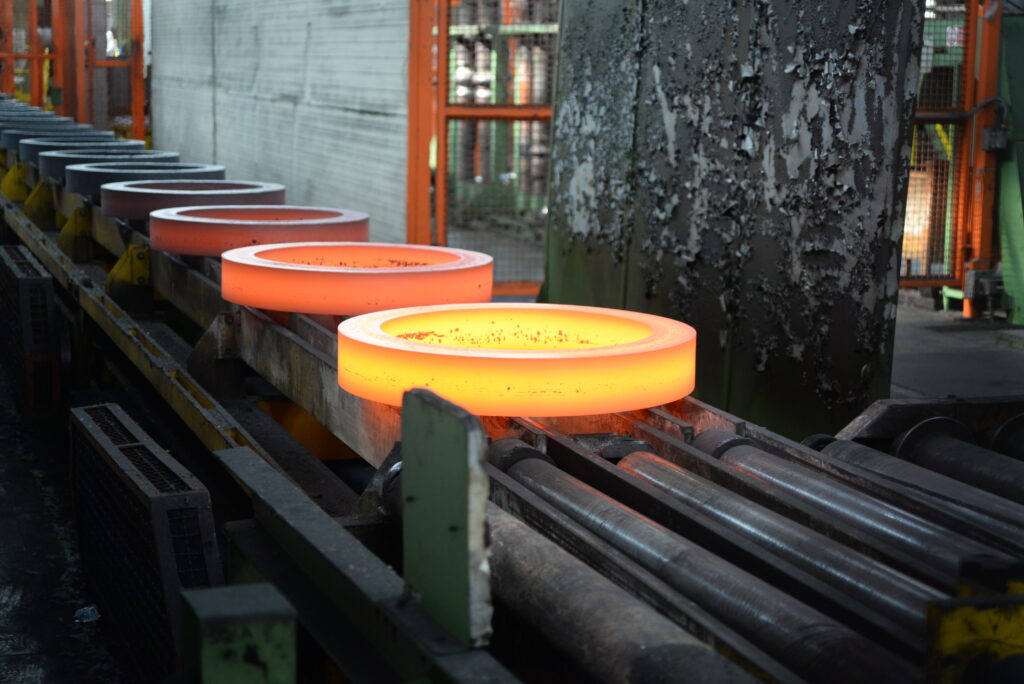
The performance of Robustus is further strengthened by another Berco innovation: BPR2. Despite Robustus having four sealing points instead of two (as occurs in the conventional design), BPR2 assures more reinforcement on the sealing points. BPR2 is a system that uses a metal ring plastically deformed as a mechanical locking element. This ring is pressed in between pin and link, locking the joint to specific predetermined end-play levels. BPR2 prevents end-play generation and increases the sealing of the joint by at least 25 percent, which leads to extended track life.
The use of the BPR2 system on conventional track group assemblies is usually recommended for heavy-duty applications such as mining, large construction, demolitions, conditions that generate large loads and impacts, twisting the chain, and generating axial movements. Even machines equipped with wide shoe arrangements can mount BPR2 in order to ensure the reduction of torsional effects on the joint. Due to all of these positive effects, BPR2 is a key ingredient for the third generation Robustus.
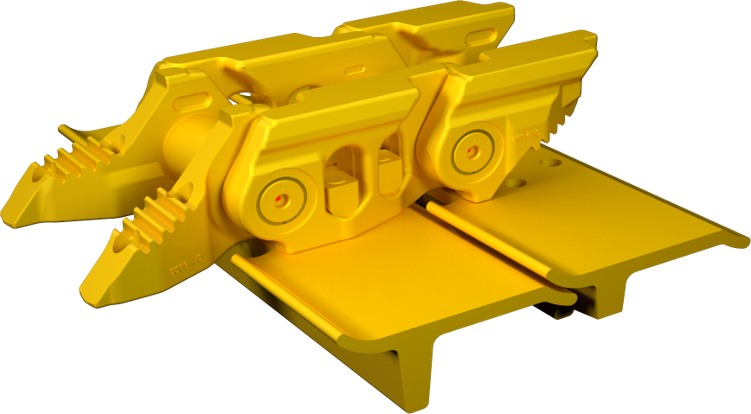
Benefits of induction hardened and tempered bushings
Another recent challenge for Berco has been that of extending the number of hours of its mining excavator application. Because of the work efficiency of the most advanced mining excavators as well as the extremely different working modes used in the open-pit mines, the goal of achieving 20,000 maintenance-free hours was indeed a difficult one.
The traveling rate of an undercarriage is also something that can significantly vary between applications. When explosions are being carried out, for example, the heavy machinery will naturally have to be evacuated from the area before detonation. In situations such as this, it is recommended to use carburized bushings, since they are the most suitable bushing type for effectively reducing the speed of wear.
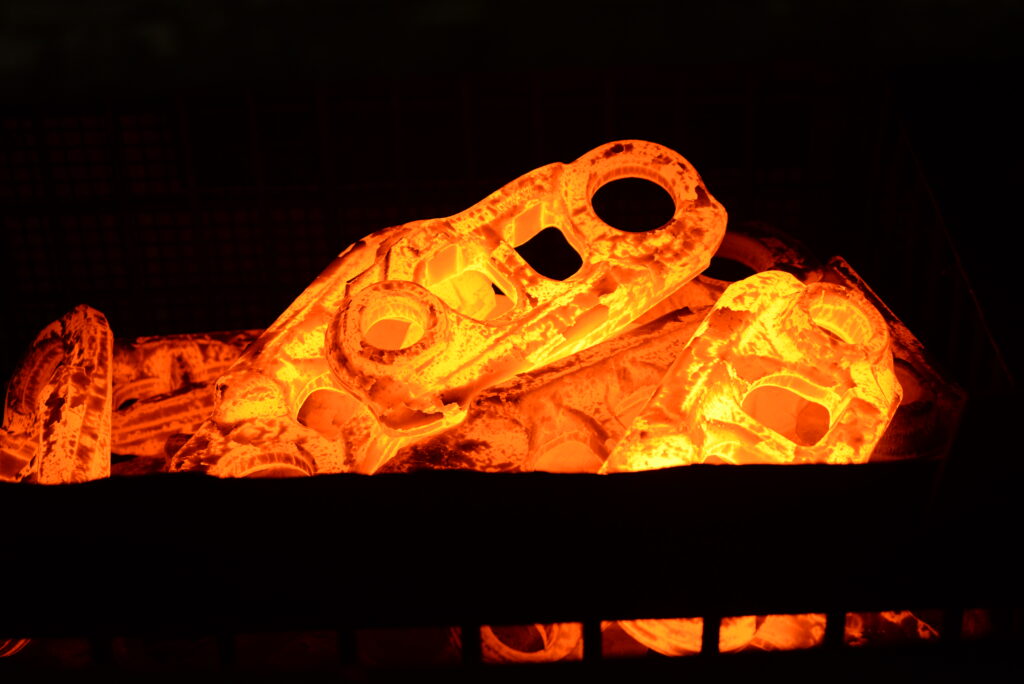
For applications that do not travel frequently, however, undercarriage parts are still often subjected to wear. The continuous hammering of the front shovel, for example, may not lead to quick wear of the bushings but can cause other side effects such as cracks on bushings. Berco’s solution, in this case, was to use both quenched and tempered, and induction hardening and tempering (IHT) bushings, as well as a quenched and tempered steel with boron which increases hardenability. These specially produced bushings deliver even more added value when fitted on reinforced chains.
This solution which is designed for heavy application such as for track chains used on 200-400t machines, provides high resistance to wear as well as outstanding resistance to impact. Being capable of achieving up to 20,000 hours of use in the field it ultimately reduces ownership and undercarriage costs. Since November 2020, they have been fitted as OE on two of the machines which the manufacturer has built to perform in Russia’s most extreme environments.
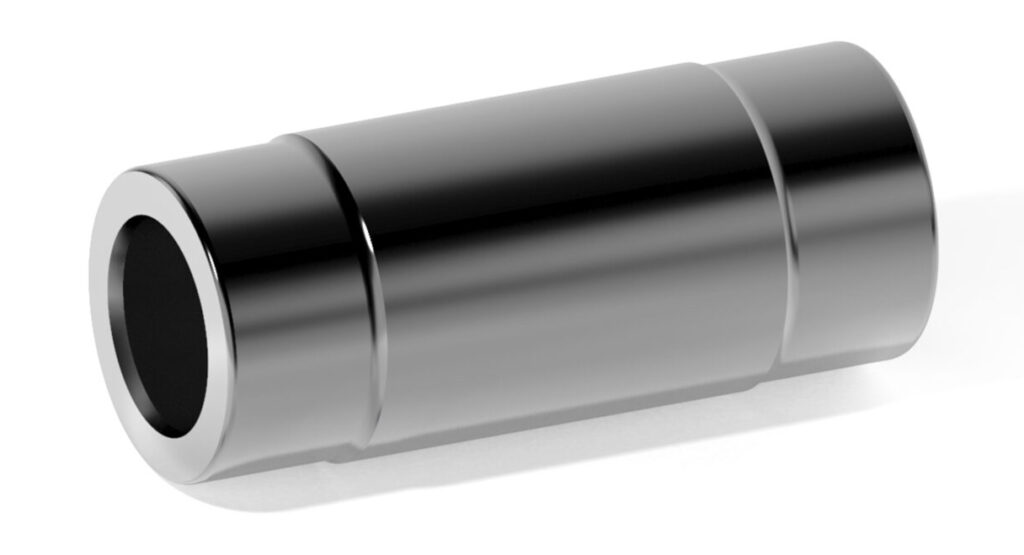
Berco’s pioneering development: rollers made from ‘rotoforged’ steel
While heavy machinery manufacturers look to Berco to cover their tailor-made solution needs, the company goes on a step further; placing a large emphasis on R&D to anticipate solutions that are ever more innovative. One perfect example of this is the use of ‘rotoforged’ steel in the production of rollers for very demanding mining applications.
This pioneering process will bring significant benefits to machines that have a huge load transfer in their working times, such as mining excavators that weigh above 200t. For applications of this size and even heavier (350 to 400t), the rollers are under particular pressure as they burden all of the inertia of the vehicle. This means that the rollers need to be made of perfect steel, which is why the ‘rotoforging’ process is an ideal solution.
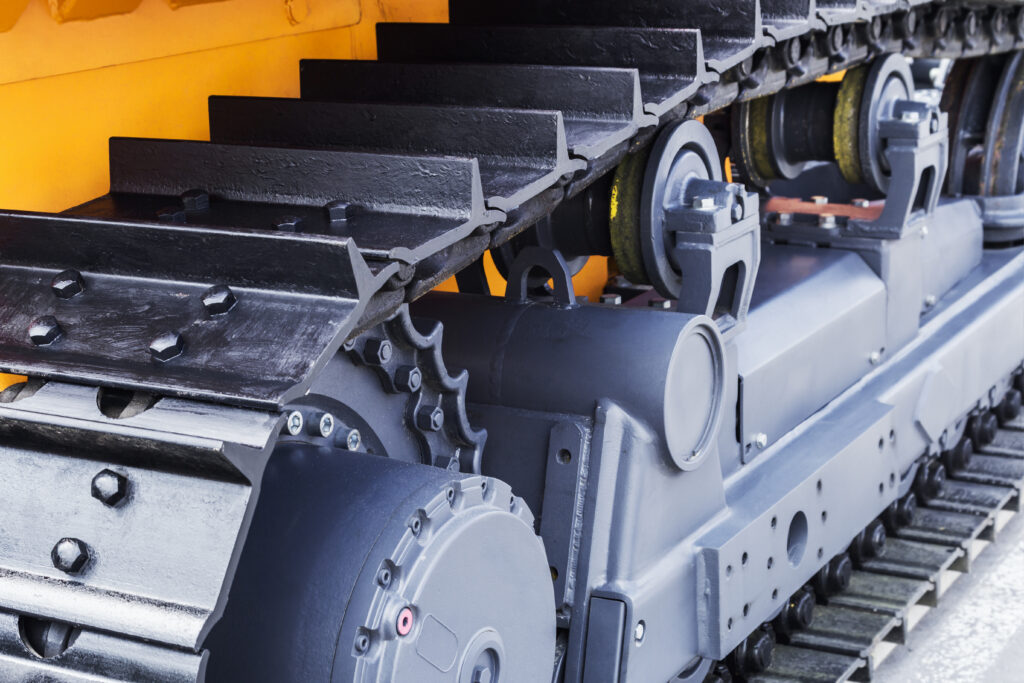
Steel that has undergone this heat treatment process acquires a high microstructure and compactness, to such an extent that it is able to achieve toughness values double those of conventional steel. Continuous casting steel is usually rolled. Rolled steel that undergoes the new ‘rotoforging’ process has its microstructure transformed down to the core, resulting in a much stronger and tougher structure.
For this reason, rollers made from ‘rotoforged’ steel are suitable for machines which must operate in the most demanding environments around the globe. They offer a very high level of reliability of between 15,000 to 20,000 hours. This innovation is now ready to enter production.
As part of the thyssenkrupp Forged Technologies Business Unit, Berco benefits from the global footprint of the Group, which ensures close proximity to all its customers. Innovative technologies and proactive forging processes situate the company at the forefront of tailor-made undercarriage solutions and services. This special know-how paves the way for Berco to become a solution provider for all future OE and Aftermarket challenges.
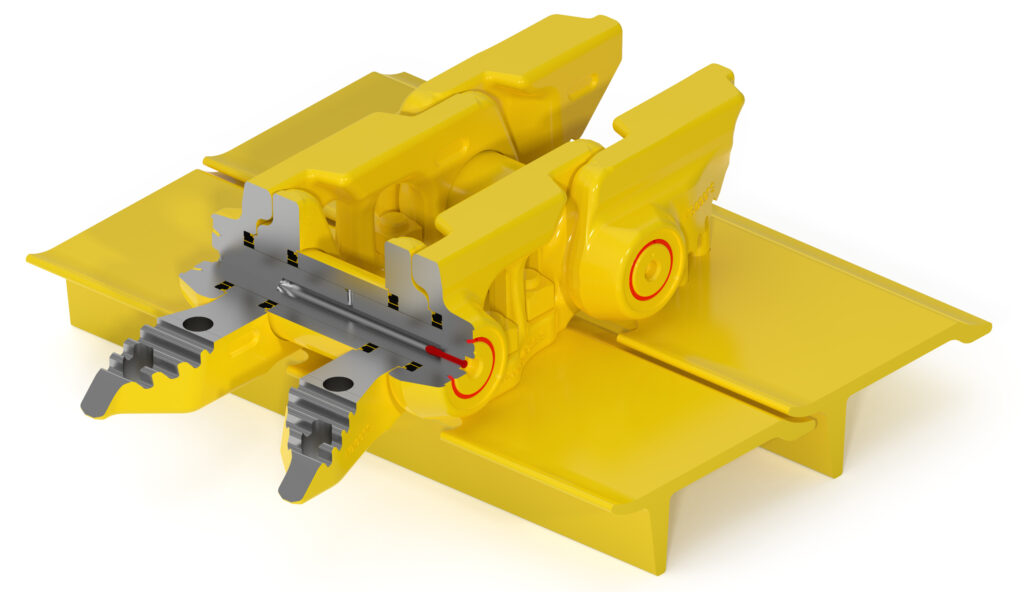