Within the range of soil processing, Wacker Neuson offers a wide portfolio of products for soil and asphalt compaction – from the vibratory rammer to the 7 metric-ton single drum soil compactor. The new walk-behind dual-vibration roller RD7 in the 700-kilogram class expands the portfolio with a unit that is particularly ergonomic and efficient in performance.

The new model generation of the vibratory roller RD7, with a drum width of 650 millimeters, delivers optimum work results on asphalt as well as on soil surfaces. The end user benefits here from easy operation via a particularly ergonomic center pole as well as tool-free access to all service points. “With the vibratory roller RD7, we are setting new standards for operating comfort,” explains Stefan Pfetsch, managing director of Wacker Neuson production.
“Our newly developed travel lever offers very intuitive control of the machine. In connection with many other machine details, this makes it easy for the operator to deliver ideal work quality at the end of the day. With different engine options and a flexible protective cage concept, we also have a suitable model variant in the portfolio for every price segment.”
Lowest hand-arm vibrations on the market
With its revised design and function, the center pole makes compacting very easy for the operator. All the operator’s controls can be reached directly on the guide handle. The travel lever, in which three different functions are integrated, makes working particularly comfortable: With this, the operator can control travel direction and the right variable speed by moving the handle forward and backward, and also stop the roller by simply releasing the handle. In addition, the travel lever is particularly easy to operate and can also be actuated easily from the side and over a longer period of time. Also, the roller RD7 exhibits, with less than 2.5 m/s², the lowest hand-arm vibrations on the market. From this aspect, too, the result is no restrictions on working time. This low vibration value means the documentation requirement is not applicable, saving contractors time. As an additional comfort plus, the vibration-dampened center pole is not set to a fixed height but can be moved freely. Due to this, the operator can effortlessly take up the most comfortable position for the moment and the respective application, which means even higher operating comfort and a reduced physical load. He doesn’t even have to run around the machine to fix the roller on a slope. Thanks to the hydraulic parking brake, the roller automatically remains reliably standing on gradients if there is an interruption in work. This results in more safety on the construction site.
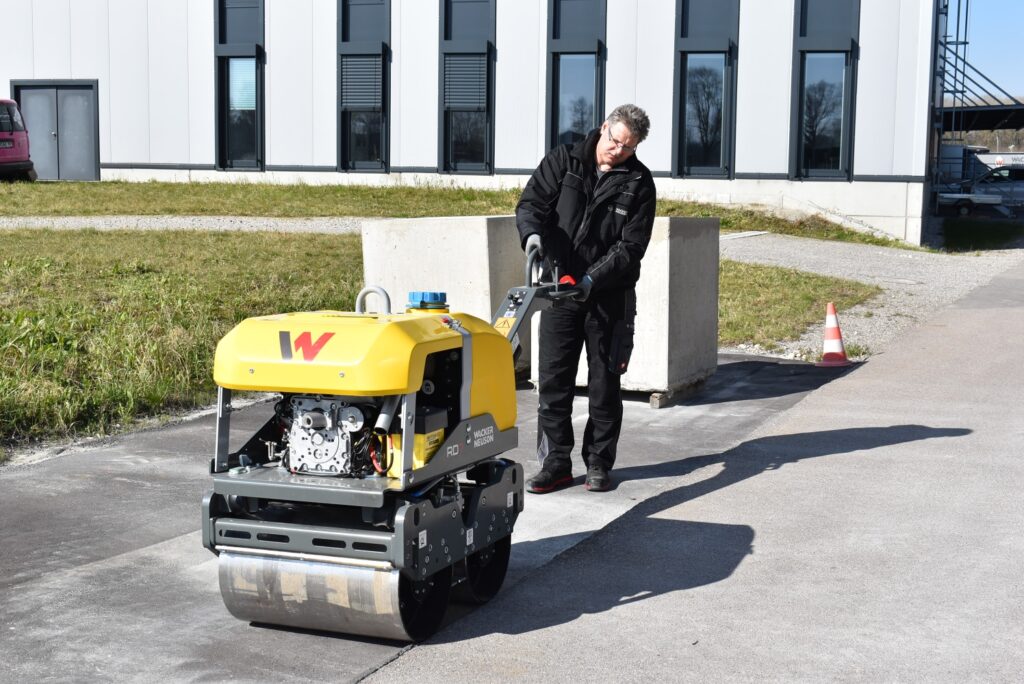
Efficient sequences of operations for optimum compaction results
The vibratory roller RD7 makes efficient sequences of operations and ideal soil compaction easy. This is ensured by the roller’s reliable straight-ahead travel and easy maneuvering. The long center pole and the resulting greater effectiveness of the lever simplify and accelerate the turning of the roller. This is also supported by the short distance between drums with a low center of gravity. In addition, the low lateral overhang of only 30 millimeters and the tapered frame narrowed at the top enable exact and uninterrupted compaction directly at walls or curbs. The dual-vibration roller with 700 kilograms operating weight is suitable for compaction of asphalt as well as for granular materials, as the vibration frequency can be optimally adjusted: the operator simply sets the vibration depending on the surface – high frequency for asphalt compaction and low frequency for soil compaction. This way, the roller RD7 achieves the required and necessary compaction and surface quality on every surface.
Easy service – higher profitability
If maintenance or repair is upcoming, reaching the most important subassemblies of the machine quickly and easily is important. In this area, the vibratory roller RD7 by Wacker Neuson scores points: the protective hood can be folded open tool-free, and all maintenance points are reachable without complications or tools. Moreover, easy access is ensured by the open design, which allows many components, such as for example hydraulic hoses, to be accessed easily. This way, downtime can be minimized, and construction site operations are not time-delayed.