In densely-populated areas in particular, the requirement for road rehabilitation to be completed rapidly is becoming more and more urgent, as job sites on busy major roads cause traffic jams. Contractor JOHANN BUNTE Bauunternehmung showed how to rehabilitate the surface and binder courses of a section of motorway successfully in an incredibly short time: on the A3 near Duisburg, the paving team rehabilitated an area of 60,000 m² in just 55 hours using four WIRTGEN cold milling machines and six VÖGELE pavers.
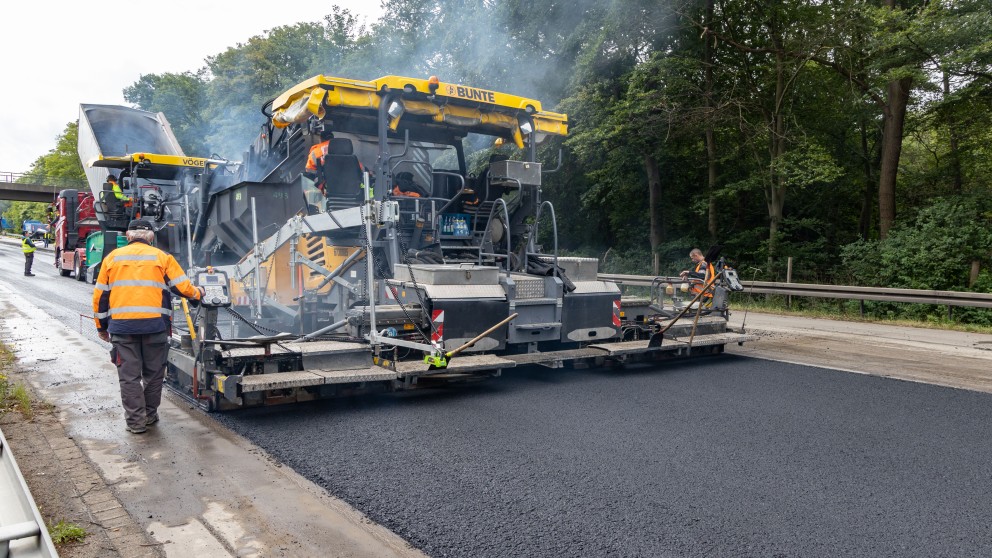
Construction projects designed to be completed in an extremely short time are demanding in many respects. They require precise planning, a high degree of process reliability and reliable machinery. Of course they also demand experience and competence from users and experts. All these parameters were important for rehabilitating a 3.6 km section of the A3 motorway near Duisburg, too. As this busy commuter route carries some 120,000 vehicles on weekdays, the responsible highways authority, Straßen.NRW, decided to carry out the rehabilitation project by closing the road completely.
“This means that in a weekend, we can complete work which would otherwise have held up traffic for several weeks – and in the end, achieve even better quality,”
says Thomas Oehler, head of department at Straßen.NRW.
The schedule was correspondingly tight: the works started on a Friday at 10 pm with a full road closure in both directions. After that, the right-hand carriageway, which is made of concrete and did not require rehabilitation, was separated from the adjacent asphalt lane using a side milling wheel. At 11 pm, four WIRTGEN cold milling machines of the W 210i, W 220i and W 250i types started removing the surface and binder courses which required rehabilitation. 20 hours were scheduled for this part of the work, and asphalt paving started before milling work was even complete – at 7.15 on the Saturday morning. Paving had to be complete by 10.30 am on the Sunday to allow enough time for follow-up tasks such as the application of road markings. The route was set to be opened to traffic on the Monday to enable commuter traffic in this densely-populated area to start the week normally.
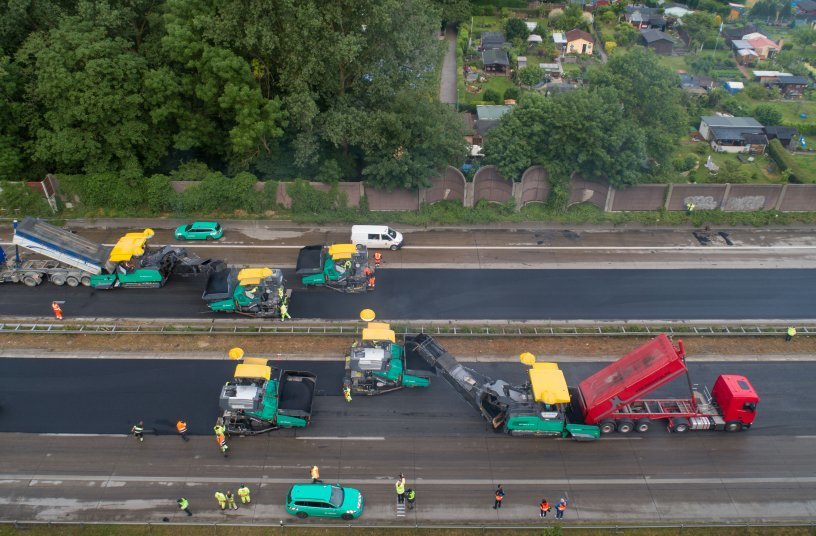
Six VÖGELE pavers in service simultaneously
A window of just 27 hours was available to pave an area of 60,000 m2. The team from contractors JOHANN BUNTE Bauunternehmung GmbH & Co. KG met this challenge with a total of six VÖGELE pavers. Two SUPER 2100-3i machines first paved the binder course. One of the two Highway Class pavers worked in one direction of travel whilst the other paver simultaneously started at the other end of the job site, working in the opposite direction. The surface course consisting of low-noise stone mastic asphalt (LOA) was then paved by two SUPER 1800-3i SprayJet machines using the “hot to hot” method.
Three mixing plants were commissioned with production of the asphalt to guarantee material supply on this very tight schedule, with a further plant in reserve in case it was needed. 130 trucks made 500 trips to transport the hot asphalt to the job site between the junctions at Duisburg-Kaiserberg and Breitscheid. In all, 16,000 t asphalt (12,000 t for the binder course and 4,000 t for the surface course) had to be produced, transported and paved.
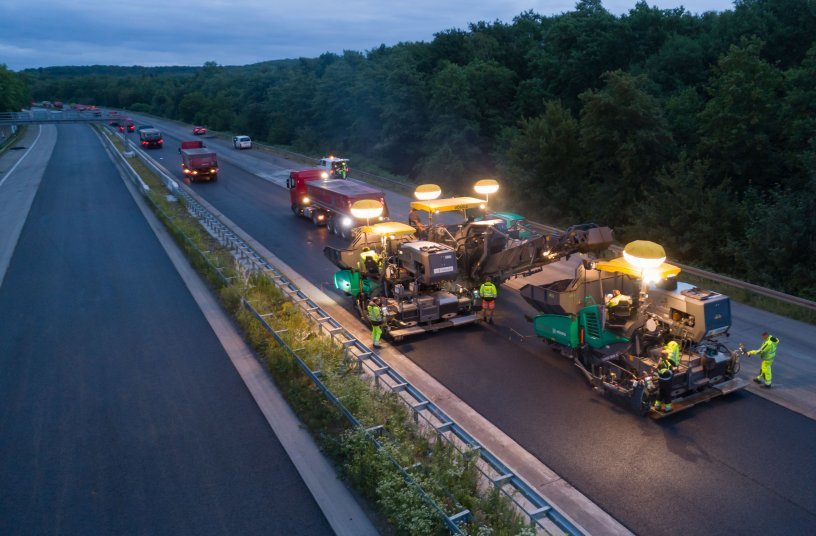
VÖGELE material feeder ensures a continuous supply of mix
Two VÖGELE PowerFeeders of the MT 3000-2i Offset type accepted the mix from the trucks to guarantee a continuous supply to the pavers. Use of two feeders was essential on this time-critical project: as the material feeder operators were coordinating unloading, this allowed the paver operators to give their full attention to the paving process. Given a whole 500 truckloads in a few hours and the high pave speeds, this was essential.
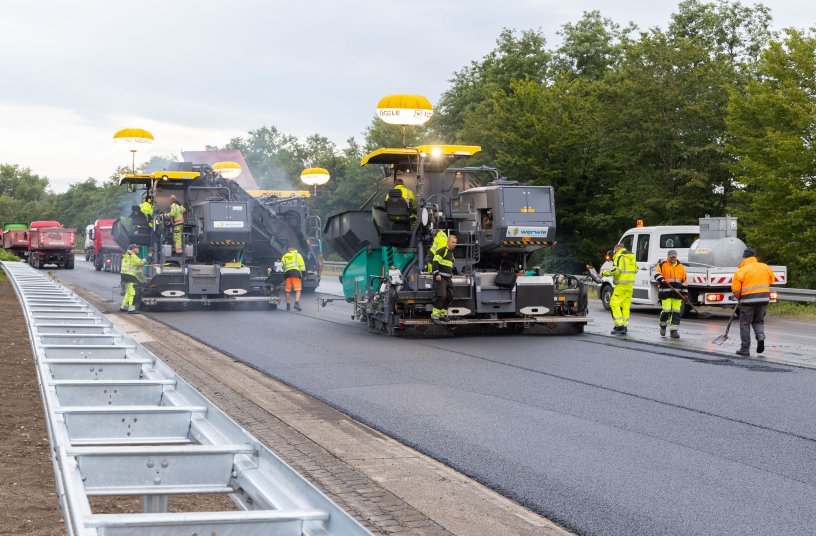
Spraying on emulsion and paving asphalt in just one operation
The VÖGELE SUPER 1800-3i SprayJet spray pavers also ensured an efficient process: they sprayed on the bitumen emulsion and paved the asphalt surface course in just one operation. In addition to saving time, paving the A3 with VÖGELE SprayJet technology had other benefits: as the freshly-applied film of emulsion was paved over immediately following application, construction vehicles were unable to drive over the binder film and damage it. This improves interlocking and thus also the service life of the road.
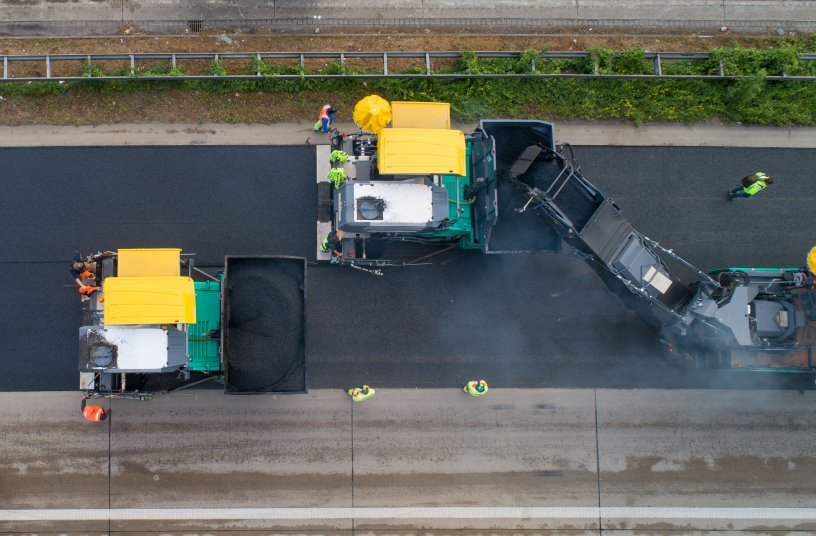
Road opened to traffic at 5 o’clock on Monday morning – objective achieved
The smooth interaction of the JOHANN BUNTE team and the machine technology from WIRTGEN and VÖGELE meant that finally, at 5 in the morning on the Monday, everything was ready: the A3 motorway was reopened to traffic. All those involved were hugely relieved to have managed the tight schedule.
“That was an incredible performance by the whole team. Everyone supported everyone else,”
said construction manager Niklas Lehmann after the project was complete.
Source: Wirtgen Group