Bucher Hydraulics and Jetter develop NIR tanker system solutions with ISOS-based precision agricultural functions. This solution allows the reduction of slurry dispersion, the reduction of nitrate pollution and promotes precision agriculture.
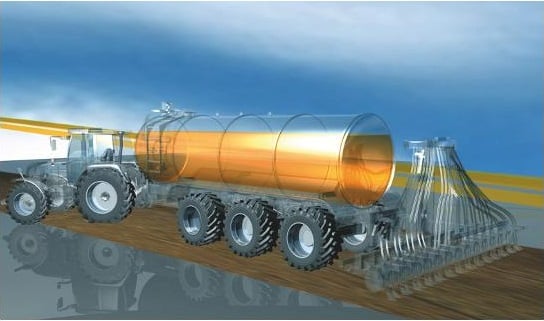
Pollution and groundwater protection
Germany has already been fined in 2018 by the Court of Justice of the EU for violating the nitrate directives in agricultural soil: about one third of groundwater in Germany exceeds the EU limit of 50 milligrams of nitrate per litre (50 ppm). This is clearly a serious problem since the drinking water distributed in the country comes from groundwater. Since 2017, the Nitrates Directive 91/676/EEC on groundwater protection is already in force, a new German fertilizer ordinance with the aim of reducing pollution.This allows farmers to apply only a fertilizer that does not exceed 60 kilograms per hectare.
Apart from the constant uncertainty as to whether the way they cultivate the soil still falls within the legal framework, the main question is whether, with their existing machinery, farmers are still competitive.
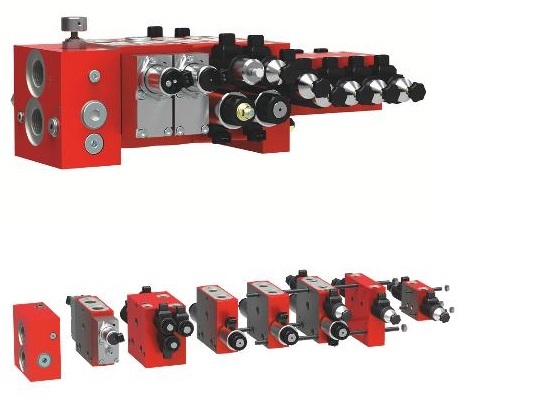
Precision Farming
For some time now there have actually been systems in place to measure soil composition and plant condition in order to calculate precisely the amount of fertiliser really needed at each particular stage of plant growth. “Precision farming’ is the name given to this procedure. It is a system that takes into account soil and plant sensors, GPS technology and special software that allows farmers to understand more about their fields than ever before. The farmer selects small areas of his field and on each of them he can carry out controls that allow him to know, for example, how much nitrogen the wheat growing there has already absorbed.
The aim is to make agriculture more and more efficient, crops optimised and collateral damage reduced. Because nutrients are not evenly distributed in the non-uniform slurry mixture, farmers are increasingly using the NIR sensor. This sensor is a small, inconspicuous box with connecting cables, mounted on the slurry pipes in slurry tankers or at filling stations. «NIR» stands for Near-InfraRed light. An NIR sensor uses near-infrared light to measure in real time the nitrogen content of the liquid manure flowing past. Based on the values measured, the required application rate is calculated and the control valve is regulated accordingly.
When fertilising soil, if the nutrients that have been added cannot be absorbed quickly enough by plants growing in the soil, rainwater transports these nutrients into groundwater in the form of nitrate. For vehicle and tool manufacturers, however, precision farming also means more and more electronic components, the integration of new sensor technologies and an increasing number of variants and functions in their vehicle range. Slurry tankers, in particular, in both self-propelled and towed versions, represent a major challenge in terms of cost and development time, as a large number of possible options must be provided in the chassis, steering system and slurry tank as well as various distribution devices.
The use of expensive high-tech sensor technologies is not cheap for everyone. But with their adaptable valve technology, Bucher Hydraulics systems enable experienced farmers to achieve high yields while complying with the nitrate rules: the very finely controllable metering valve with intuitive operating concept, combined with the farmer’s wealth of experience, ensures precision metering at low cost.

The slurry tanker system solution jointly developed by Bucher Hydraulics and Jetter is «NIR-ready», i.e. already included and configurable as an option. All precision farming functions based on the ISOBUS are already «on board». These include Virtual Terminal, the integration of a tractor ECU, a freely configurable joystick, Task Controller BAS, the application rate that is specific to a particular sub-area using Task Controller, Section Control and Task Controller Geo.
Generic modular development
The approach of Bucher Hydraulics and Jetter AG has been to completely end the “serial” development process that starts with equirements specifications, then project planning, engineering, prototype procurement, test phase and initial sampling: The design of the system solution was broken down into a number of individual modular solutions, taking into account all common variants and technologies on the market. This was true for both the hardware and the software aspects. For this purpose, an interdisciplinary team of ucher and Jetter engineers defined more than 40 hydraulic subfunctions for the slurry tanker. The “generic system solution for slurry tankers” contains around 1400 parameters. Each specific overall system for a particular slurry tanker now consists of a combination of selected and previously tested and optimized subsystems.
Source:Bucher Hydraulics