All asphalt production businesses want to minimise the cost of ownership. The lower those expenses, the more competitive asphalt prices can be – and the higher profits can go.
Ammann’s efforts to reduce asphalt operating expenses include two key products that protect plants: Ammlub and Amdurit
Ammlub

Ammann’s automatic lubrication system provides three key benefits: longer plant life, reduced fuel costs and improved safety. Traditional lubrication methods often require that technicians stretch and strain to reach extremely tight spaces – and that they fight dust, dirt and heat in the process.There also is the question of when to grease – and how much grease to apply. Was it too much? Not enough?
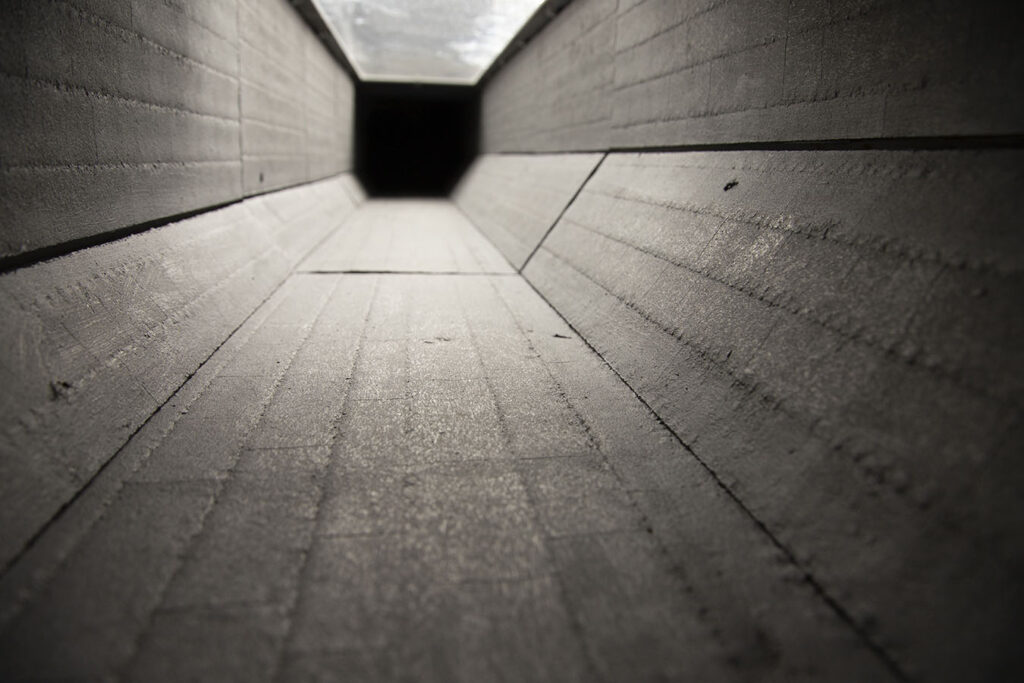
The labor-saving, smart system Ammlub is mounted directly on the plant’s lubrication points. It automatically applies lubricants at scheduled intervals, ensuring that the process is done on time – every time.
In addition, Ammlub eliminates downtime. The lubricant applications can occur while the plant is running, enabling completion of the routine maintenance without a drop in productivity. An immediate benefit is fuel savings, which can be reduced as much as 10% when all parts and components are working harmoniously.
With appropriate lubrication, those parts and components will also last longer, providing further savings. Because this system also locks out contaminants, plant life is extended, too. Workplace safety is improved as well. Technicians no longer need to lug tools and fluids with them to access difficult-to-reach service points.
These service points typically include all components along the process flow, starting with the cold feeder and ending with the discharge shoot-
Amdurit

When looking for ways to lower operating expenses, don’t forget about the value that results from properly protecting a plant.
Amdurit, Ammann’s proprietary wear-protection system, provides up to 3 times the service life of wear-resistant steel and protects valuable parts and components.
It makes maintenance easy, too. Instead of replacing the component, simply swap out the Amdurit covering. The wear-protection system results in savings on multiple fronts: components last longer, which translates to fewer replacements and therefore lower costs; in addition, plant owners also avoid the labor costs associated with replacement of the components.

There are many potential areas of use, including drum inserts; transition and discharge locations; feeders (both RAP and traditional); and silos. The preferred areas of use with regard to components for reclaimed asphalt (RAP) feed are:
- RAP elevator feed and discharge
- Drum pipe infeed, cone and scales in the drum pipe
- Intermediate container and chute in the mixer
- RAP feed, worm screw and screw trough
Source: Ammann Group