Stand 415 Hall A2
SIKO, a player in position sensor systems for mobile machines, will demonstrate how its innovative and reliable sensors support the development of autonomous and highly automated construction machines.
SIKO will showcase a comprehensive range of sensor solutions designed for mobile machines. Whether addressing new safety standards, complex motion control, or innovative application concepts, the company’s products are tailored specifically for mobile machine applications, ensuring maximum reliability, safety, and advanced technology.
Focus on Functional Safety: Enabling Secure Autonomous Machines
Safety remains a top priority for SIKO, as reflected in its extensive portfolio of safety position sensors. These products meet the highest safety standards and contribute to the development of future-proof applications.
“Safe position sensors, also referred to as safety sensors, have been an integral part of our product portfolio for 20 years and remain a focal point of our exhibition booth this year. Construction sites are complex environments where a variety of machines operate in close proximity to people. With highly automated and autonomous machines, prioritizing safety requirements is essential. Our goal is to support customers by providing powerful and reliable sensor solutions.”
stated Mathias Roth, Manager of the Mobile Automation Business Unit at SIKO.
SIKO designs robust, application-oriented sensor solutions for mobile machines as a strategic development partner. With a deep understanding of industry requirements, the company offers support from the planning stage through to sensor implementation. The extensive product portfolio includes both standard solutions and systems customized to specific operational needs.
Among the latest innovations that SIKO will present at Bauma 2025 are:
NEO Series Draw-Wire Encoders. Measuring lengths from 3 to 15 meters, these encoders feature a compact design, exceptional durability, and safety functions up to Performance Level d (PLd). What was initially introduced as a prototype at Bauma 2022 in Munich has now been developed into a market-ready product in time for Bauma 2025. The NEO series represents the next generation of reliable, compact, and safety-focused draw-wire sensors, designed for applications in demanding environments such as construction machinery, industrial trucks, and crane and lifting technology. At Bauma 2025, sensor specialist SIKO will showcase this new series of draw-wire encoders, which were originally presented as a concept and have since undergone significant refinements based on customer and industry feedback. The NEO series highlights advancements in wire-actuated encoder technology, reinforcing SIKO’s expertise in this field.
About the platform behind the NEO series, which stands for “New Electronic Options,” is built upon the latest iteration of SIKO’s PURE.MOBILE sensor platform. Specifically developed for mobile machine applications, this platform integrates contactless magnetic measuring technology, ensuring a wear-free operation. Additionally, the mechatronic multiturn system used in these sensors requires neither a battery nor an external energy source, making it both highly reliable and maintenance-free over extended periods, even in extremely low temperatures. The NEO series consists of multiple models tailored to different measurement needs:
- SG31NEO – up to 3.2 meters
- SG61NEO – up to 6 meters
- SG121NEO – up to 12 meters
- SG150NEO – up to 15 meters
These sensors incorporate well-established draw-wire mechanics, ensuring high operational performance in mobile machines. Features such as a variety of wire options, ice formation prevention measures, multiple wire fixation choices, and robust sealing and temperature architecture contribute to their durability. The sensors are engineered to function reliably in temperatures as low as -40°C and in consistently wet conditions.
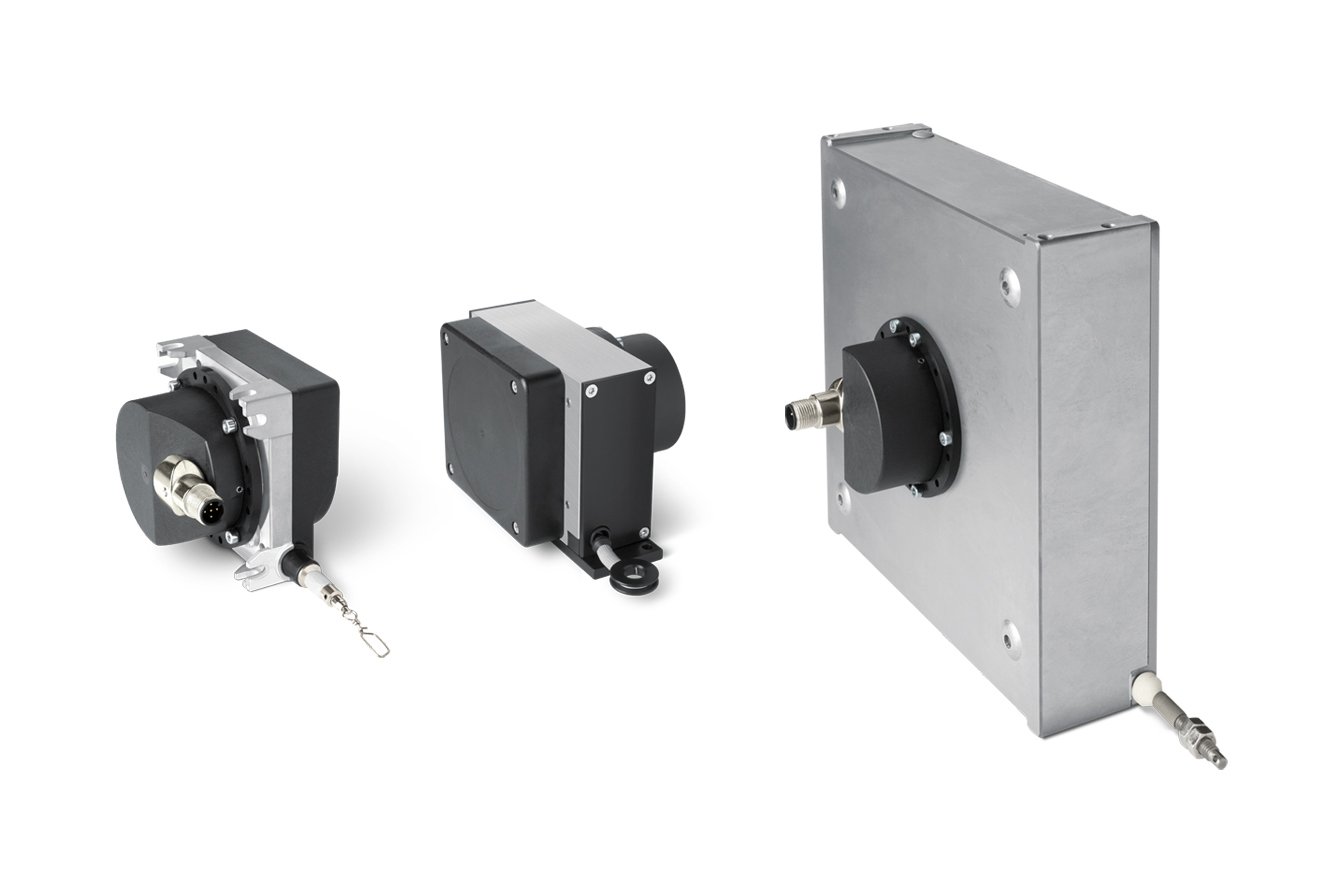
IMS365R Inertial Measurement Unit (IMU). Certified to SIL2 and PLd, an advanced inertial measurement unit (IMU) designed to provide high-precision measurements in dynamic applications while withstanding extreme environmental conditions. Developed specifically for mobile machine automation, the IMS365 marks a significant advancement in position measurement, offering not only inclination, gyroscope, and acceleration data but also new measurement capabilities such as Euler angles. The IMS365 integrates a Kalman filter and a high-performance sensor fusion algorithm, which effectively reduce disturbances from lateral acceleration, shocks, and vibrations, ensuring accurate inclination readings even in highly dynamic environments. These features make the IMS365 well-suited for applications such as excavators, autonomous guided vehicles (AGVs), agricultural and forestry machines. The fast response time and enhanced measurement accuracy enable precise automation processes.The IMS365 measures inclination, acceleration, and rotation rates across all three spatial axes, ensuring comprehensive position data at all times. A distinctive feature of the device is its ability to perform measurements independently of the installation position, with the ability to automatically adjust measurement axes according to the application’s requirements. For enhanced performance in varying environmental conditions, the IMS365 includes an integrated heating element, which can be activated or deactivated via the interface as needed. This ensures consistently high measurement accuracy and reliability, even in environments with extreme temperature fluctuations.
The sensor is available with CANopen and SAE-J1939 interfaces, facilitating seamless integration into control systems. The IMS365 is a highly adaptable sensor, capable of supporting a wide range of applications.
Excavators: provide stable and precise position values even during rapid movements and shocks when handling bulk materials.
AGVs and Autonomous Systems: supports accurate navigation with a high-quality signal and minimal offset drift, ensuring long-term reliability without requiring system restarts.
Agricultural Machinery: improves efficiency in automatic levelling and blade section adjustments for enhanced productivity.
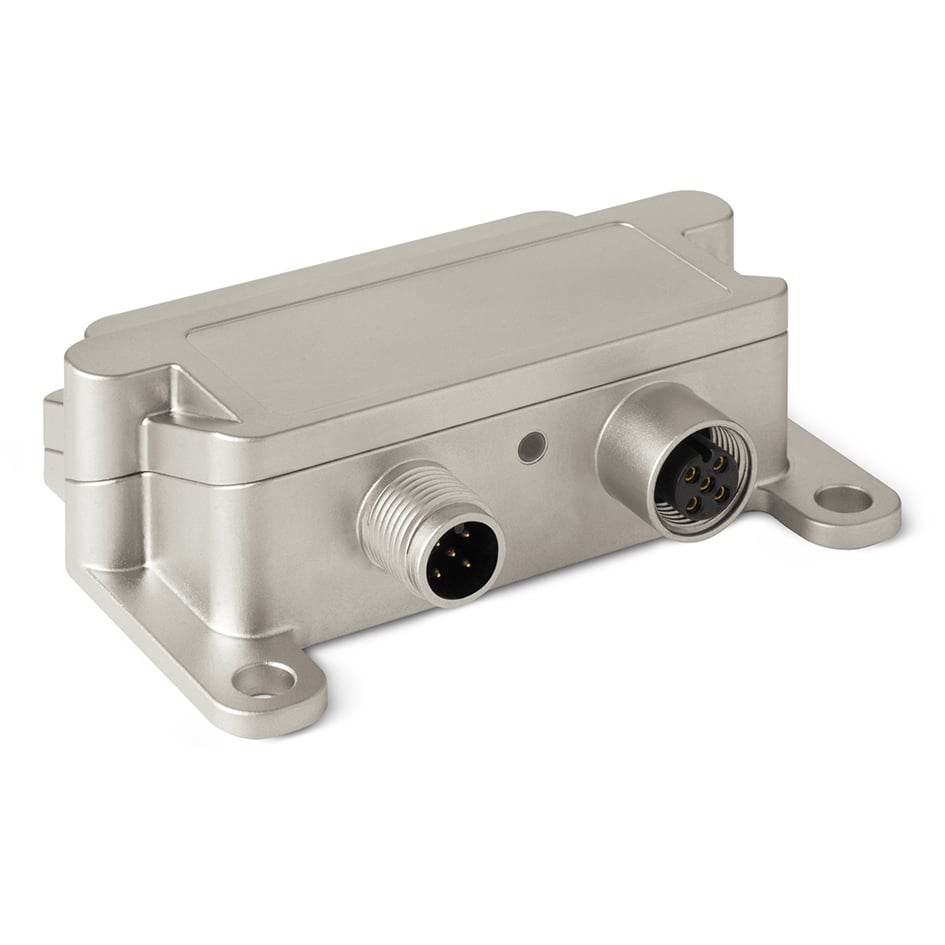
WV3600MR & WH3600MR Absolute Multiturn Encoders. The world’s smallest safe absolute multiturn encoders, offering precise position and speed data with a compact 36mm diameter design. The WV3600MR and WH3600MR are ultra-compact absolute safety multiturn encoders designed for mobile machines, providing precise position and speed data while ensuring compliance with SIL2 (IEC 61508) and PLd (DIN EN ISO 13849) safety standards. With a diameter of only 36 mm, they are among the smallest of their kind and feature a measuring range of up to 65,536 revolutions (16-bit resolution). Built on a contactless magnetic measuring system, these encoders operate without batteries, ensuring a maintenance-free and long-lasting performance in demanding environments.
Engineered for harsh conditions, they are highly shock and vibration-resistant, withstand axial and radial shaft loads up to 200 N, and feature IP67 or optional IP6K9K protection ratings, UV resistance, and a salt-mist-resistant housing. Certified under E1 (UN ECE R10), they are approved for use in road-based mobile applications.
For enhanced system integration and monitoring, the encoders support CANopen Safety, with future compatibility for SAE J1939-76 (Safety). Additional smart functions enable real-time status monitoring. Their flexible installation options, including axial or radial connections with M12, DEUTSCH, or AMP Superseal plugs, make them highly adaptable for construction, industrial, and agricultural machines. By combining safety, durability, and smart connectivity, the WV3600MR and WH3600MR contribute to efficient and reliable automation in mobile machinery.
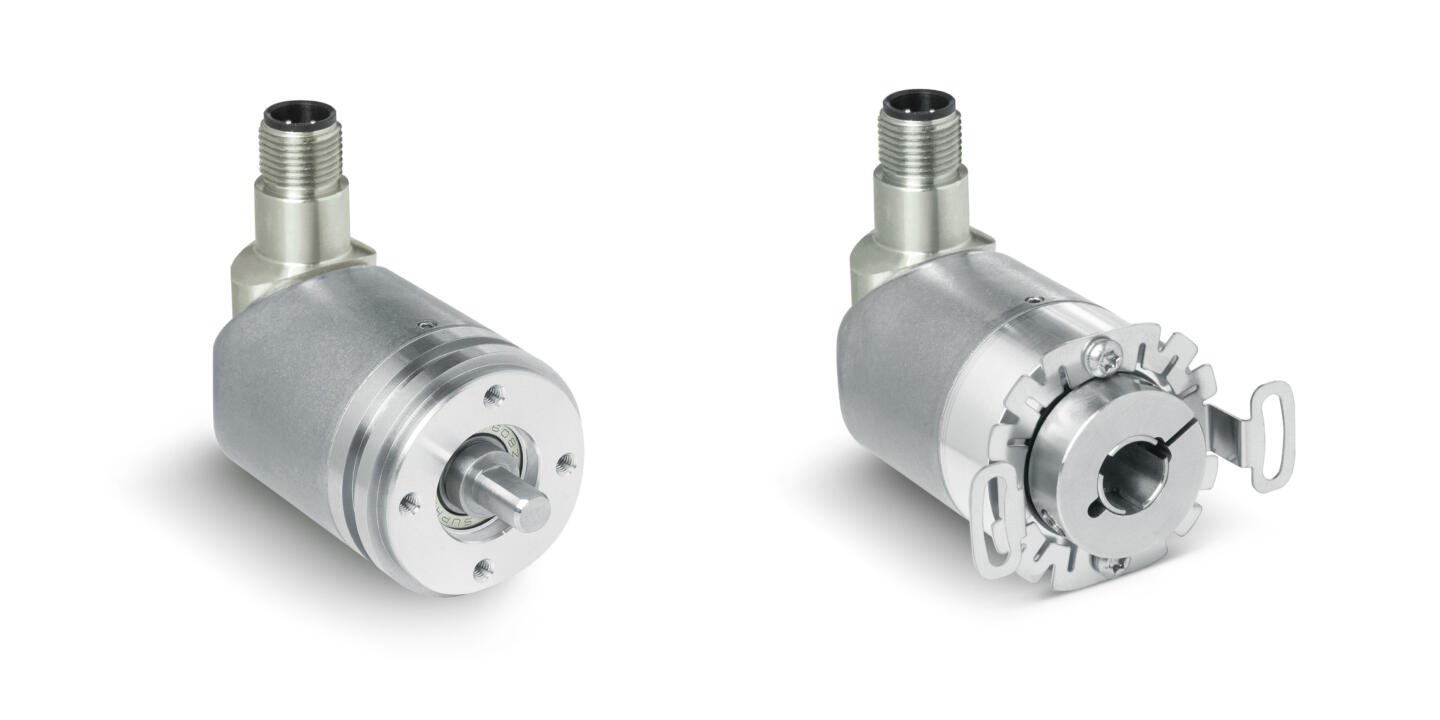
Another notable innovation is the MSK5000CAN Bearingless Encoder, featuring a compact design and high protection rating (up to IP68), making it ideal for contactless speed, travel direction, and position detection. This encoder transmits data via a CANopen interface for seamless integration. The MSK5000CAN is a bearingless encoder designed for mobile automation applications, offering high precision, robustness, and cost-effectiveness. Equipped with advanced magnetic measurement technology and a CANopen interface, it provides accurate speed, direction, and position data, making it well-suited for construction, agricultural machines, industrial trucks, and AGVs.With a maximum resolution of 5 μm and repeat accuracy of ±0.01 mm, the MSK5000CAN ensures precise motion control, while its fully cast electronics and high IP protection safeguard it from water, dust, and extreme environmental conditions. The compact, bearingless design allows easy integration into existing machines, reducing installation space requirements and eliminating maintenance needs. By combining precision, durability, and seamless connectivity, the MSK5000CAN offers an efficient and reliable solution for modern automated and autonomous mobile systems.
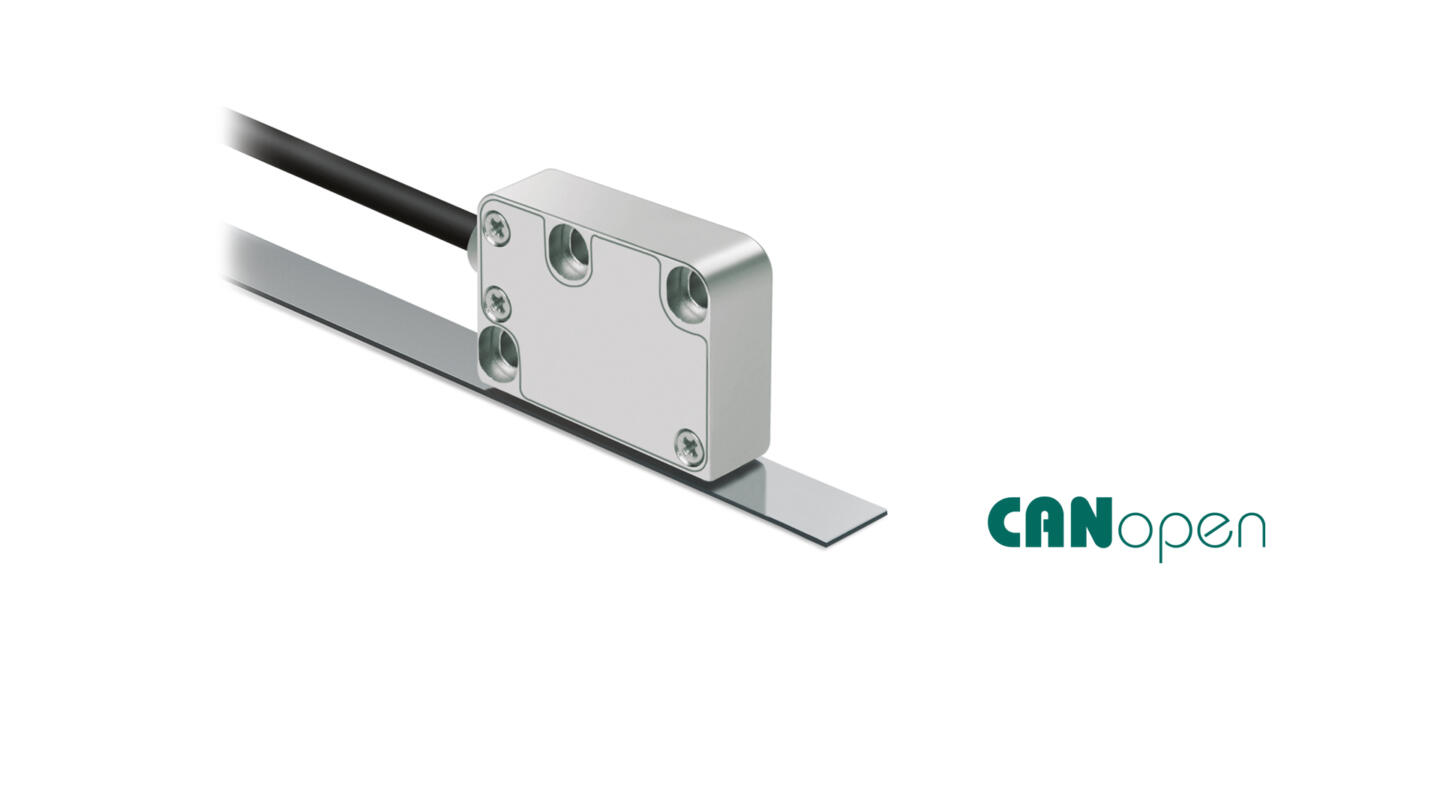
Additionally, the MSAC200 Bearingless Encoder, also known as FlexCoder, stands out for its versatility and ability to accommodate various hollow shaft diameters up to 230 mm. Designed for use in electric drives, slip rings, and hydraulic motors, it offers resolutions of up to 20 bits per rotation. The MSAC200 FlexCoder, a bearingless, fully magnetic encoder, now integrates CANopen for enhanced compatibility with electric drives, power gearboxes, and mobile machine powertrains. By providing precise speed and position data, it supports efficient system control, reducing energy losses and optimizing performance.Designed for steering and drive systems, the MSAC200 ensures accurate control of powertrains, aiding in steering angle monitoring, speed measurement, and reliable position feedback—even after power failures. Its compact design allows easy integration into space-constrained environments, while FlexCoder technology supports hollow shaft diameters up to 230 mm with high installation tolerance.Built for OEM applications, the MSAC200 delivers robust performance even in extreme temperature conditions, making it ideal for powertrains, slip rings, winch systems, and other mobile machine components. Its high precision, durability, and flexible installation contribute to reliable automation in dynamic applications.
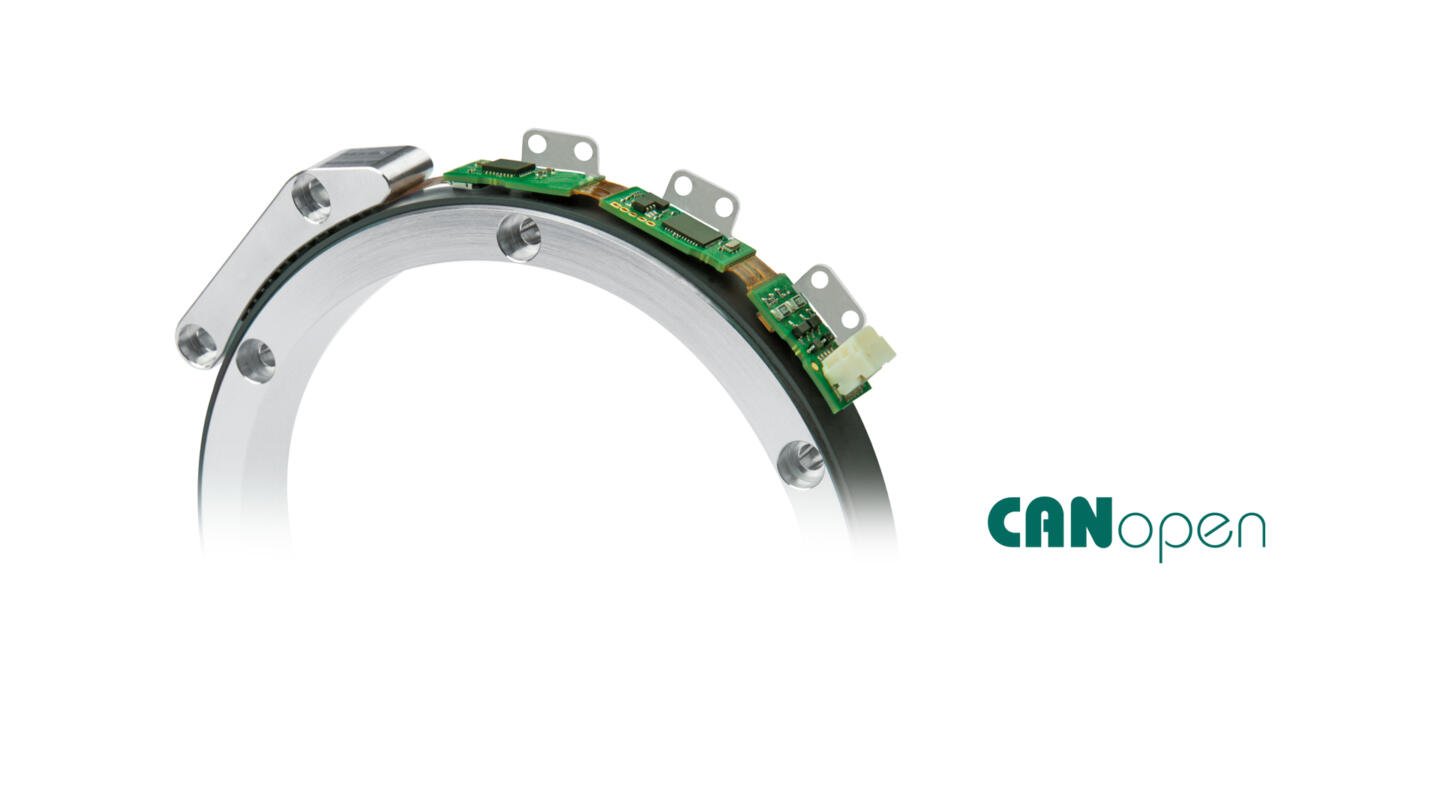