Two sites from a single location – whilst preparing explosives to demolish a coal-fired power station in Lünen, North Rhine-Westphalia, the Liebherr mobile crane was working on another site at the same time due to high time pressure.
Fitted with a luffing lattice jib with a maximum length of 91 metres, the new LTM 1650-8.1 from Bergheim-based crane contractor Wasel GmbH had to hoist explosives experts up to a platform on the chimney of the decommissioned power plant at a height of 140 metres. Façade components on the boilerhouse also had to be removed at the same time using radii of up to 80 metres.
For crane operator Michael Müllers, this job with his new Liebherr crane was not exactly a comfortable one. The experienced crane operator in the cab of the LTM 1650- 8.1 had to work on two sites at the same time for this demolition project. At the foot of the 250 metre chimney at the former coal-fired power plant, the crane was responsible for hoisting the explosives crew together with their drilling gear and explosives up to a work platform on the flue at a height of around 140 metres. Once there, they placed around 30 kilograms of explosives in 140 boreholes. As a result of its enormous height, the giant chimney could not simply be demolished by placing explosives at its base, and instead it had to be demolished using a single-folding method.
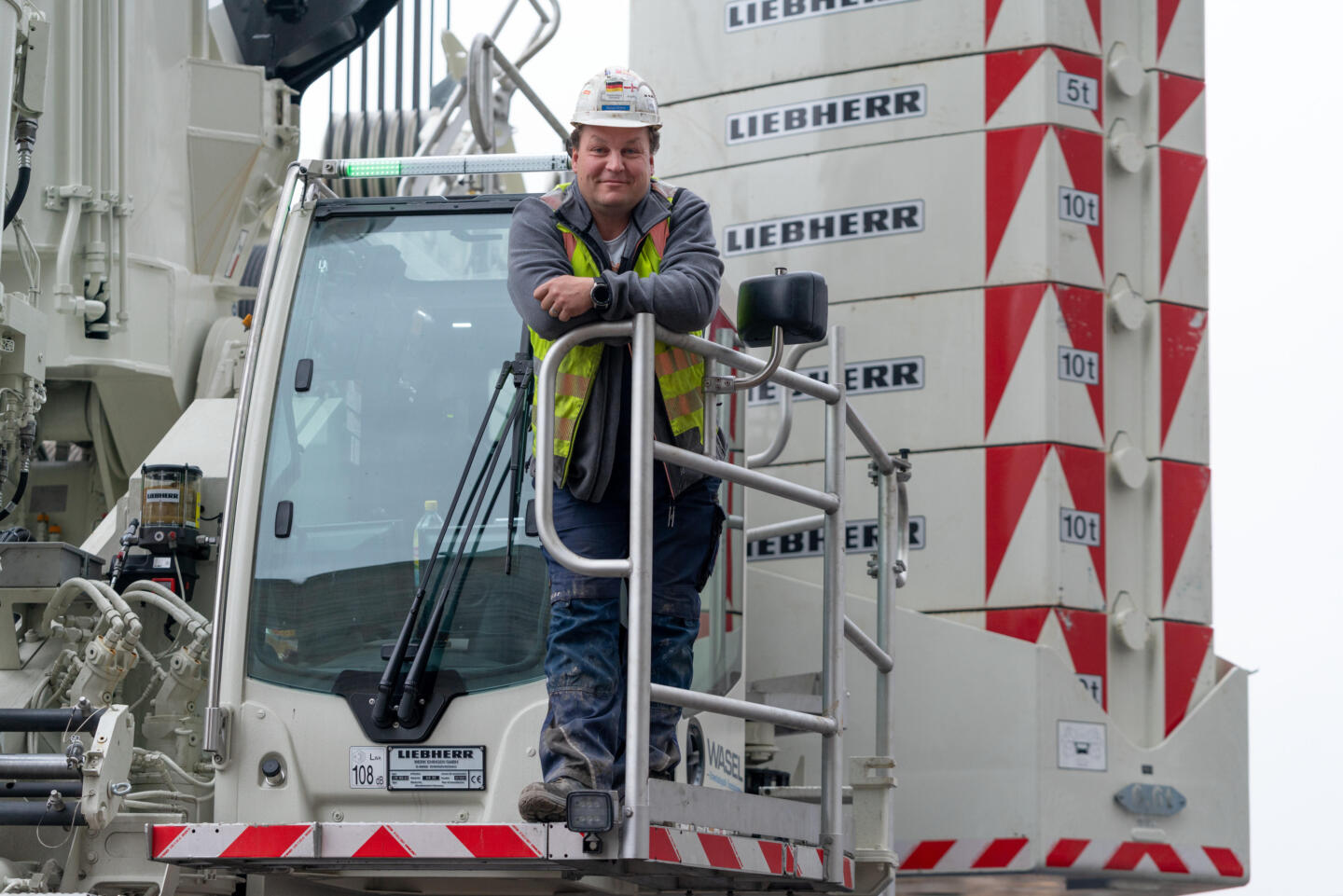
Required flexibility delivered by VarioBallast
The Liebherr crane had a total of 145 tonnes of slewing platform ballast to enable it to support the demolition work on the façade of the neighbouring building from the same location. Using its 91 metre luffing lattice jib, it was able to reach even the furthest points to help dismantle the façade. A large platform which held a team of workers and the salvaged material was hoisted in full over the neighbouring 70 metre high building. The platform was then used on the other side of the building at radii of up to 80 metres. The safety cage, personnel and demolition material created a gross load case of around eight tonnes for the powerful mobile crane with its impressively long luffing jib. To manage this large radius, Michael Müllers set the radius of the slewing platform ballast to the maximum value of 8.4 metres. For working on the chimney with radii of around 45 metres, the ballast distance simply had to be reduced to 6.4 metres using the hydraulic slewing mechanism.
Mandatory equipment – hydraulic unit for emergency take down
A hydraulic unit was also on the site in the immediate vicinity of the crane in case of emergency. When working with safety cages and work platforms on the crane hook, a unit of this type is mandatory so that if the crane engine suffers a failure, the safety cage can be lowered safely at any time. However, it was not needed on the former power plant site. The crane, which, in fact, also has an integral emergency take down system of its own, functioned perfectly throughout the job which lasted several weeks.
After around six months in the operator’s cab of the LTM 1650-8.1, crane operator Michael Müllers is extremely satisfied with his new machine. Wasel GmbH is based in Bergheim near the River Rhine and, in addition to crane work, also provides heavy logistics, tower cranes and industrial assembly services. To date, the company has mainly used its new crane in refineries, for handling heavy goods and for jobs in industry.
“The crane’s handling is really good, particularly setting it up. And as far as lifting capacities are concerned, it represents a real quantum leap forwards. It’s a fantastic machine.”
says Müllers about the ease of use of the modern mobile crane.