“The excavator has to work”, that is what Helmut Lyko, machine operator at Stolte in Bottrop, expects from his work machine, a Cat wheeled excavator M314 of the new generation. He is the first in Germany to put it into operation. The driver has been working with the construction machine in road construction since October 2020. It offers a smooth operation on the construction sites in the Ruhr region and, above all, it has become more comfortable.
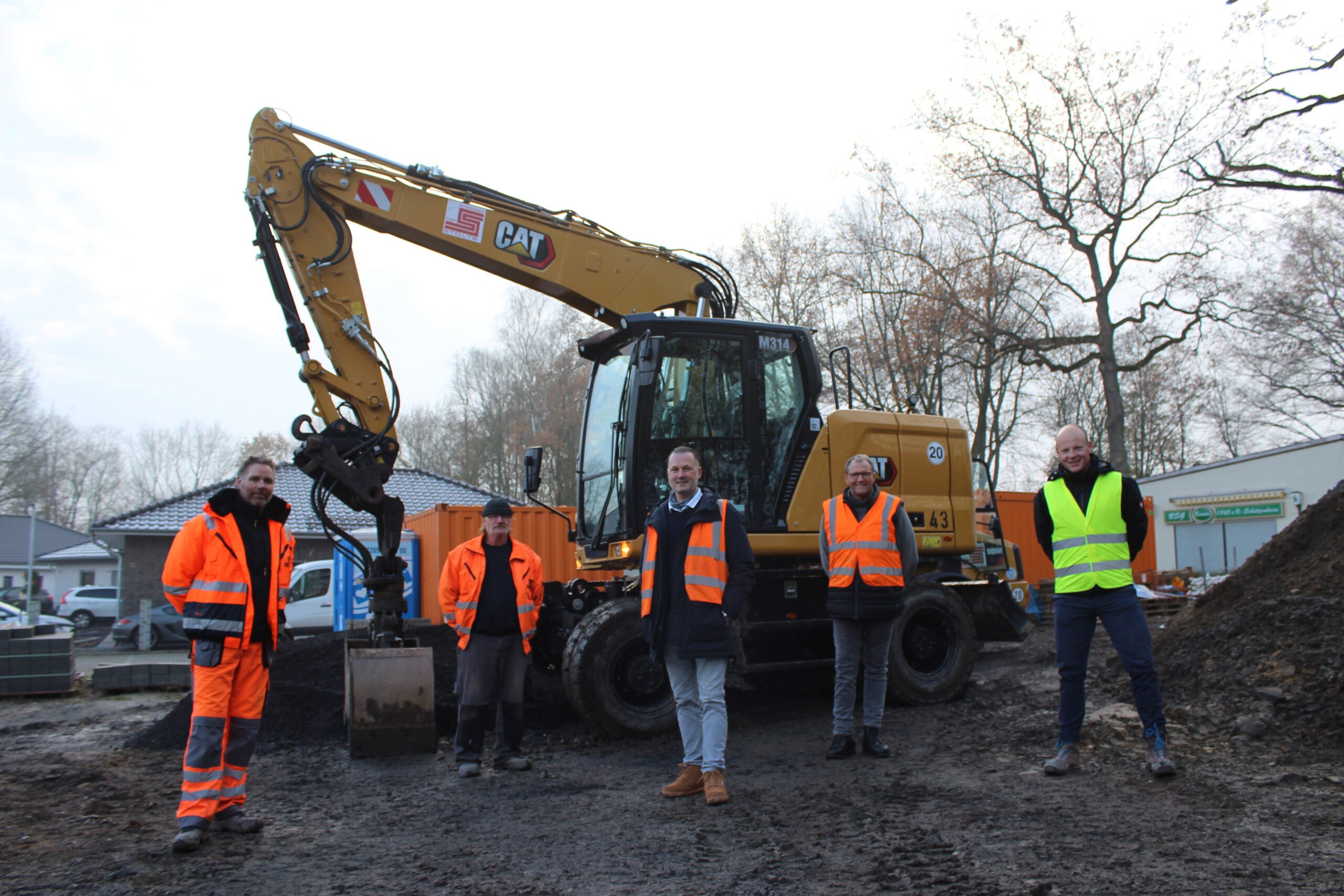
“The new excavator is easy to operate, the essential functions have remained the same” is the driver’s verdict. He now sits in a larger and newly developed operator’s cab, just like the one already offered by the new tracked excavator generation. A flat engine bonnet and a large front, rear and side windows that allow improved visibility around the machine, something Helmut Lyko also appreciates. From his old M313D he was familiar with the reversing camera: now a side camera has also been added as standard, giving him a better overview of his working environment.
This is currently in Marl, where the construction company has to take on a wide range of tasks in road construction with the mobile excavator. The requirement profile includes moving and spreading soil. The construction machine is also used to lay out a subgrade, if necessary, and it must be able to break up the road surface. The company uses small and large pavers, which have to be loaded by the excavator in the same way as the trucks used.
“The construction machine is an essential auxiliary tool on the construction site and thus a true multifunctional tool” says managing director Kay Stolte.
The driver can access deep and ditching buckets as well as grapples. Thanks to the quick-change system, they can be attached quickly without Helmut Lyko having to get out of the car for a long time. Helmut Lyko selects functions and settings for the required work steps via the touchscreen monitor and the jog dial input. The automatic axle lock also controls the locking of the service brake, which also simplifies operation. A significant innovation for machine operators such as the Stolte employee is the electrohydraulic pilot control of the joysticks. Drivers can now select the response behaviour themselves according to their preferences and also save it. Helmut Lyko prefers the classic average value: “That’s enough” he says.
“Almost 80 per cent of all riders prefer the medium setting, while the the remaining 20 percent choose the harder or lighter mode. This means that every rider has the
the machine to best suit his needs,” says Marc Patalong, Zeppelin Product Manager Standard Equipment, who is responsible for the wheeled excavator product group.
wheeled excavator product group.
A separate slewing pump enables up to 15 percent more slewing torque compared to the predecessor series and creates fast working and loading cycles. “I have not yet been able to consciously notice more slewing torque” admits the excavator operator.
The reasons for this have to do with the work application: “This has more of an effect when working with it on a slope and is swivelled against the slope” says the Zeppelin product manager.
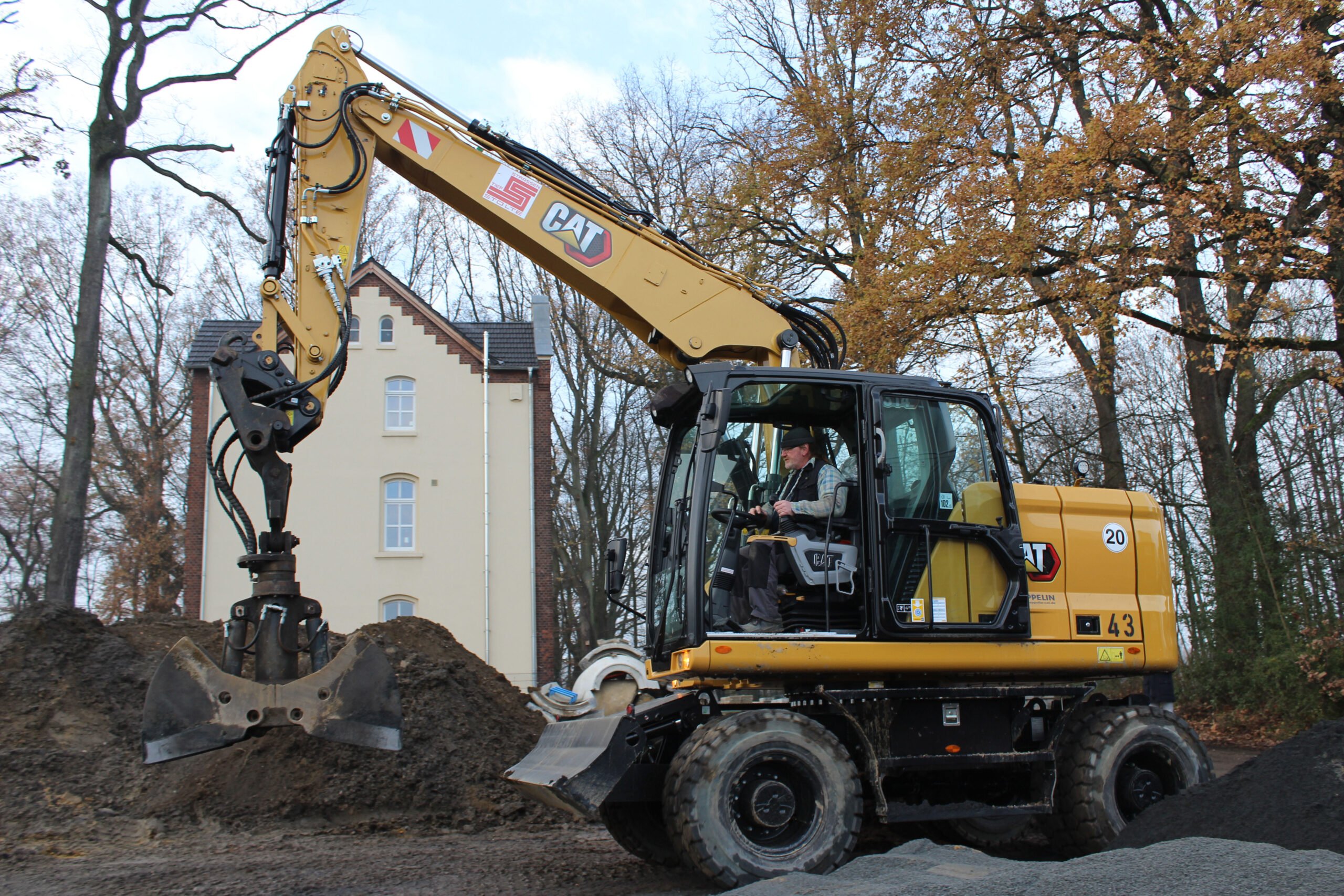
Kay Stolte also sees the fact that fewer maintenance costs will be incurred in the future as positive. What’s the reason for this? Filters have a longer service life with the new generation of machines – like the doubling of the life cycles of the air filter sets. This was not yet the case with Helmut Lyko’s machine. By December, the excavator had completed about a hundred hours of operation. In order to display data such as operating hours, fuel consumption and location, Kay Stolte accesses the fleet management system and uses the Vision Link application – currently from a PC, but in the future he could imagine using a tablet to data analysis.
“This will become more and more of an issue in the future,” he is convinced. “The most helpful thing is to precisely coordinate and plan the timing of maintenance,” says Kay Stolte.
New remote diagnostic tools on the Cat M314 can help save service trips to the construction site. This is because Zeppelin service technicians can use them to perform diagnostics to identify potential problems by analysing real-time machine data without having to travel to the site. If they have to work on the excavator, they have the required spare part with them. “In the case of less serious problems, there may be no need for a mechanic to go out, but the driver can fix them if he gets a tip or two about which bolt he needs to tighten with which torque” the company boss hopes.
Stolte’s machine park includes a whole range of Cat wheeled excavators, from the
M314F, M315D, M316F, M318D and M318F up to the M320F. In addition come no fewer Cat wheel loaders, starting with a 906H2, 906M, 907H, 908H2, 908M and 914M. They are used for road, asphalt, earthwork, sewer and civil engineering work, which is carried out for private customers, municipal and commercial clients within a radius of 50
kilometres around the company’s headquarters in Bottrop. Together with the company MBS GmbH from Marl, which focuses on clients from the chemical industry and
refineries, the company employs around 90 people and one of them is Helmut Lyko: the driver of the latest mobile excavator.