The combination of Vögele and Witos products proved successfully: the team from Georg Koch GmbH used the construction project in Wilhelmshaven as an intensive opportunity to get to know Vögele’s networked system solution for process optimization and documentation.
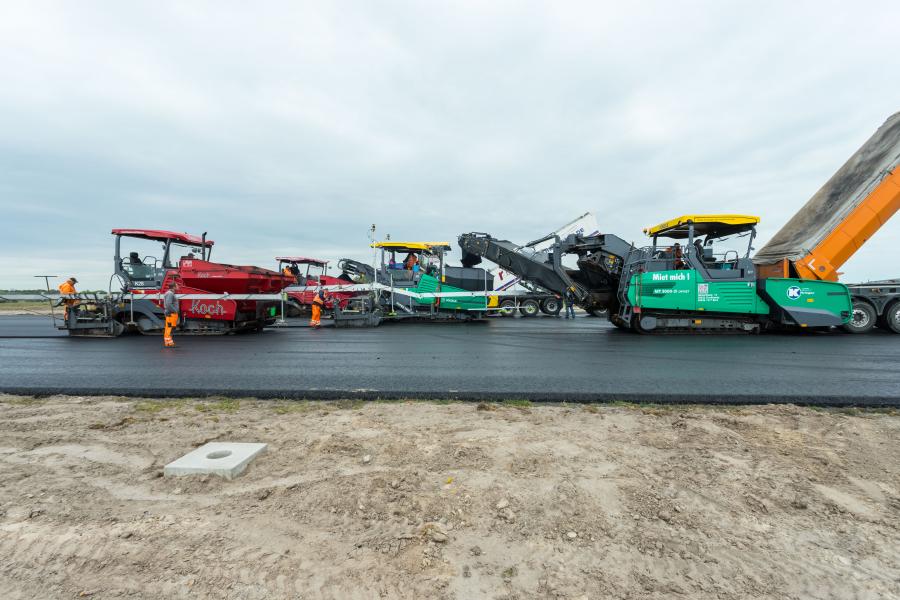
The technology of Vögele enabled the pavers to operate continuously, while Witos Paving Plus achieved incredible results in terms of time and increased productivity.
The asphalt work consisted of paving the runway, approximately 1,500 m long. A SUPER 1900-3i – equipped with Witos Paving Plus – was used as the primary paver to pave two asphalt base courses (pre-profile and base course). For the final paving operation, namely the surface course, three SUPER pavers worked “hot to hot”.
Asphalt paving without joints and with crown
The asphalt runway at Jade-Weser Airport consists of two asphalt base courses and one surface course. The lower courses were paved by a SUPER 1900-3i. This tracked paver was equipped with Witos Paving Plus. The primary paver was supported by a SUPER 1600-3i and a SUPER 1800-3i for the final paving stage, the surface course. The machines worked “hot to hot” with an overlap of around 20cm – and thus without joints.
The paving strips were selected so as not to create a centre joint: the SUPER 1900-3i worked a width of 7.5 m in the centre of the runway and paved a crown. Beside it, the two other Vögele pavers paved two strips with a transverse slope, creating a width of 15 m.
The primary paver finally paved the outer strips, making a total width of 30m. The fact that it was possible to work practically continuously throughout was due not least to the use of Witos Paving Paving Plus.
Added value with a cash value
After all, the implementation of the project only confirmed the initial estimates already made by the Witos system: according to the system, 13 mix trucks were needed on the first paving day to supply the three Vögele pavers with mix.
The analysis system makes it possible to obtain statistics and documentation about the means and materials needed for the project. This enables construction projects to be assessed objectively and enables contractors to learn from each day’s paving operations and gain information for the next day.

Exceeding the expectations of Kock’s group, which had estimated the use of 15 trucks, the only 13 truck mixers calculated by the Witos Paving Plus system were enough: this meant saving a lot of money, no interruptio on work or be slowed down.
Thanks to the five different Witos Paving modules network, the supervisors at the asphalt mixing plant, the truck drivers from the transport company and the whole paving team on site are connected each other all the time. The system gives planning engineers and site managers a full overview of the current project. Therefore, potential disruptions and obstacles to the construction process are picked up more quickly, which gives those involved more options for dealing with them. Staff are put in a position where they can take immediate measures to optimize the job site and remedy deviations from the planned workflow in real time.
Ease of operation is at least as important as accurate function
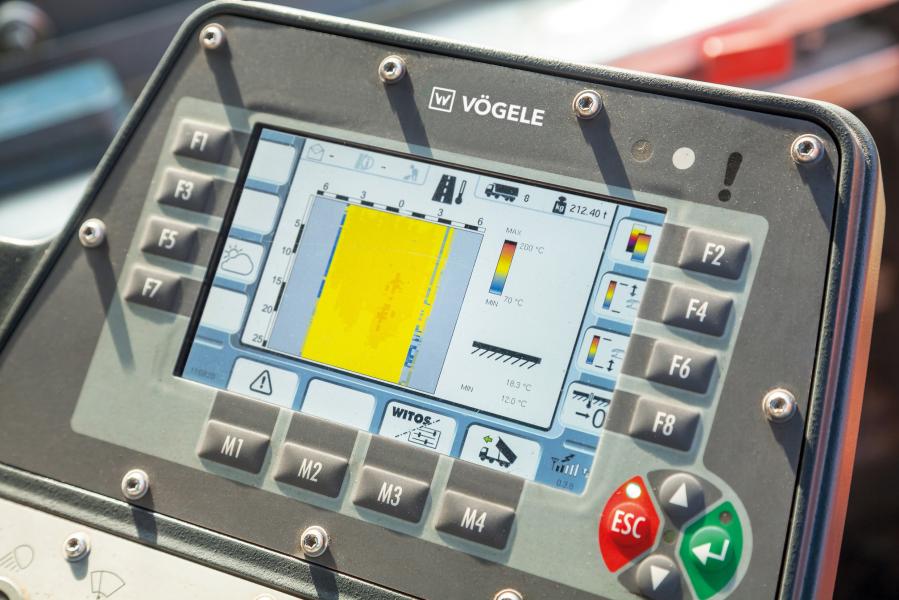
“Witos Paving is extremely practical. It can simply be used, whatever the weather. The software functions are easy to understand. As a result I was quickly able to see what key added value the system offers. I wouldn’t want to be without it now,”
insisted works supervisor Theo Hülsmayer, who operated the Witos Paving Paving Plus JobSite module on an outdoor PC on the job site itself. This visualized all the key paving parameters for him on a tablet or outdoor PC.
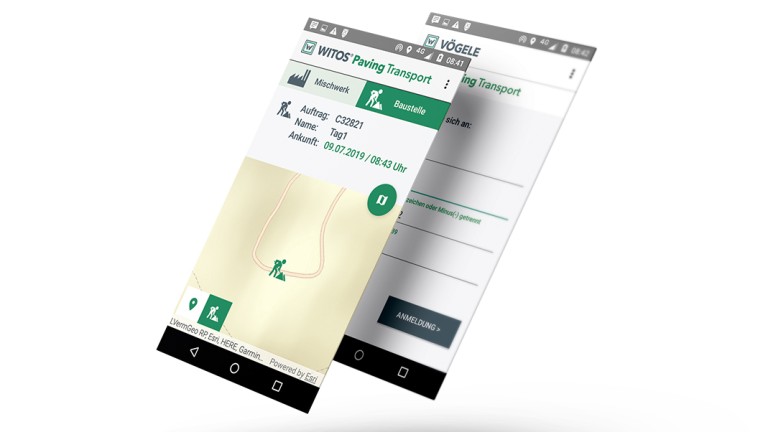
”The system impressed us a lot right back at the planning stage, because it simply calculated a lot of the values itself – for example, the quantity of asphalt required. If the capacity of the planned mixing plant is too low, the system issues a warning,”
said Tim Gassmann. This allowed to manage easierly the jobsite and arranged a second mixing plant in good time to cover peak demand.
Source:Wirtgen Group